Embracing the Future: How the Manufacturing Industry is Adapting for the Gen Z Workforce
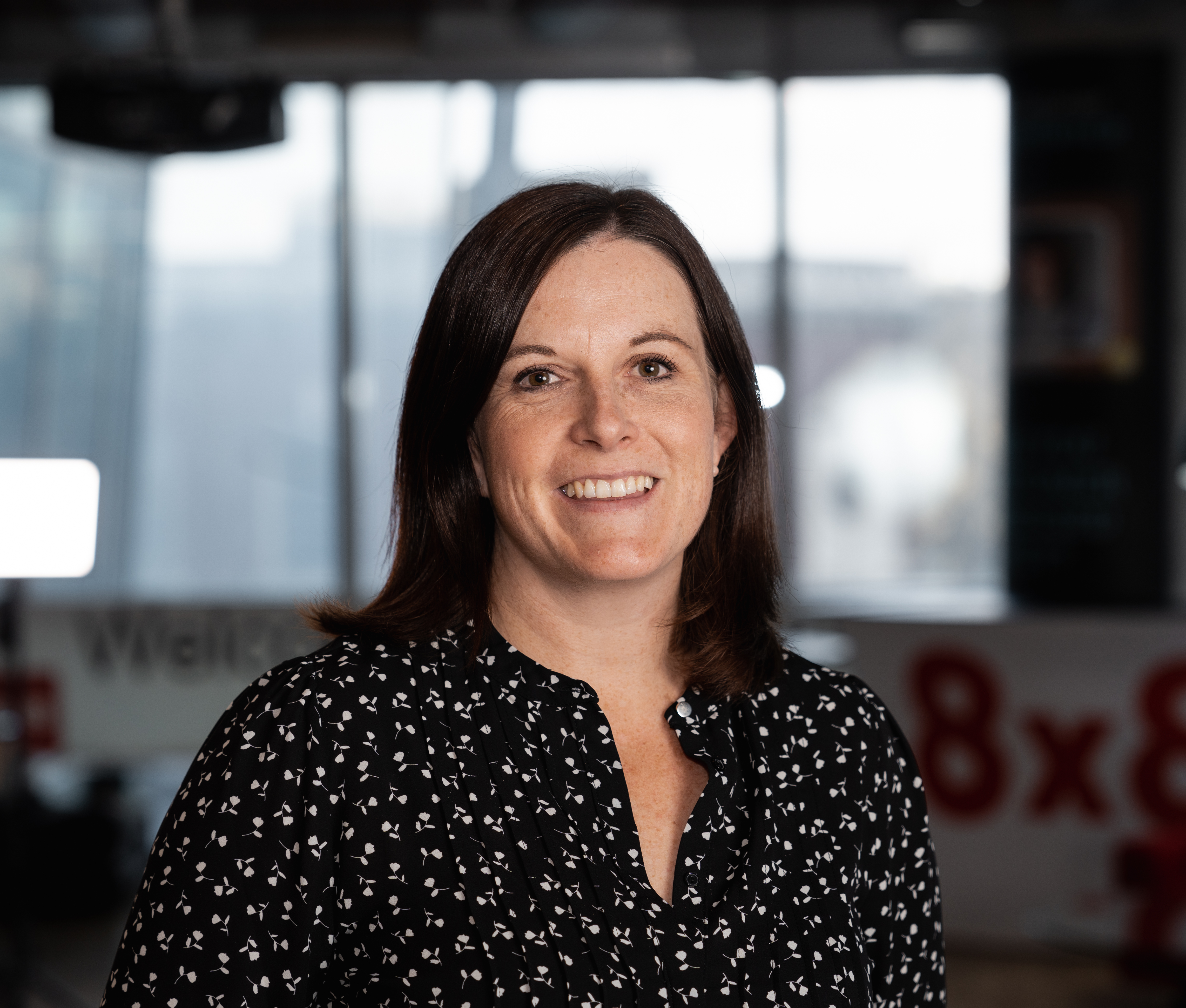
In today's manufacturing landscape, a significant shift is underway. Generation Z is entering the workforce, bringing distinct preferences, goals, and challenges to employers in this sector. As the baton is passed from one generation to the next, the industry must adapt—not only attract this new wave of talent but also retain them.
On top of this, manufacturing is experiencing a wave of change driven by increased funding and the adoption of new technologies. This shift, often referred to as the Fourth Industrial Revolution, is revitalizing productivity growth.
Here's a closer look at how manufacturing is evolving to meet the needs and expectations of Gen Z workers.
Nurturing a unique set of challenges
Gen Z workers present unique challenges. Studies show that they are not drawn to traditional assembly line and frontline worker roles which can often be deemed as repetitive and lacking engagement. A staggering 48% expressed an intent to leave their manufacturing jobs within the next three to six months.
Unlike previous generations, Gen Zers prioritize factors like meaningful work and workplace flexibility above compensation. When choosing roles, career development and doing more meaningful work are important to them. Some manufacturers that have begun investing in nurturing these employees’ careers have yielded significant results, with their staffing levels rising by 25% and production improving by 20%.
Addressing attrition and the shift to gig-working
Attrition rates among Gen Z workers in manufacturing are alarming and highlight the need for proactive retention strategies. While wage increases have been implemented in response to past labor shortages, they haven’t fully addressed the 43% gap between job openings and hires since January 2020.
Korn Ferry has predicted a 7.9 million employee-sized hole by 2030, across the sector and so a shift to short-term, contract-based employees will be needed to fill the gap. And maintaining productivity while training new employees and getting contract workers up to speed presents numerous challenges for employers.
In light of all this, manufacturers must focus on creating compelling workplace cultures with technologies that foster loyalty if they want to retain Gen Z talent.
Increasing points of engagement
Gen Zers are digital natives and will make up over 58% of the workforce in the near future. It’s essential that manufacturers adapt to their way of thinking, because the ways manufacturers historically engaged with employees won’t work anymore. For example, many Gen Z workers are used to learning from watching videos online, and they may feel uncomfortable asking coworkers for help in person.
To engage Gen Z workers effectively, manufacturers must:
- provide skills development opportunities that merge digital and analog learning methods
- facilitate interpersonal relationships with experienced colleagues where they are supported across multiple communication channels
Flexibility as a solution
According to an 8x8 Contact Center Report, 49% of Gen Z workers say they’ll quit if their employer doesn’t give them work flexibility. This got some forward-thinking manufacturers to:
- adopt workplace scheduling
- eliminate long shifts to accommodate employee preferences
- use insightful tools to assist in workload forecasting and scheduling
Apart from scheduling flexibility, top floor workers working with customers are looking at operationally efficient ways to communicate with the shop floor workers, who are often too busy to take calls.
Implementing collaborative work apps, like 8x8 Work, can empower employees to communicate by messaging their colleagues’ mobiles on the shop floor. This gives them a quick and easy way to respond at a time that suits their availability.
Manufacturing a better tomorrow
The manufacturing industry stands at a crossroads, ready to adapt to the needs of its evolving workforce. By investing in development, offering flexibility, and fostering an inclusive culture by introducing solutions that will allow them to engage, collaborate and communicate effectively, the industry will attract and retain Gen Z talent, ensuring sustained success.
Investing in development, offering flexibility, and fostering an inclusive culture ensures that the industry will attract—and retain!—Gen Z talent. Introducing solutions that allow them to engage, collaborate, and communicate effectively is a step toward sustained success with this new generation.
Download our eBook to explore other workforce trends affecting the manufacturing industry.